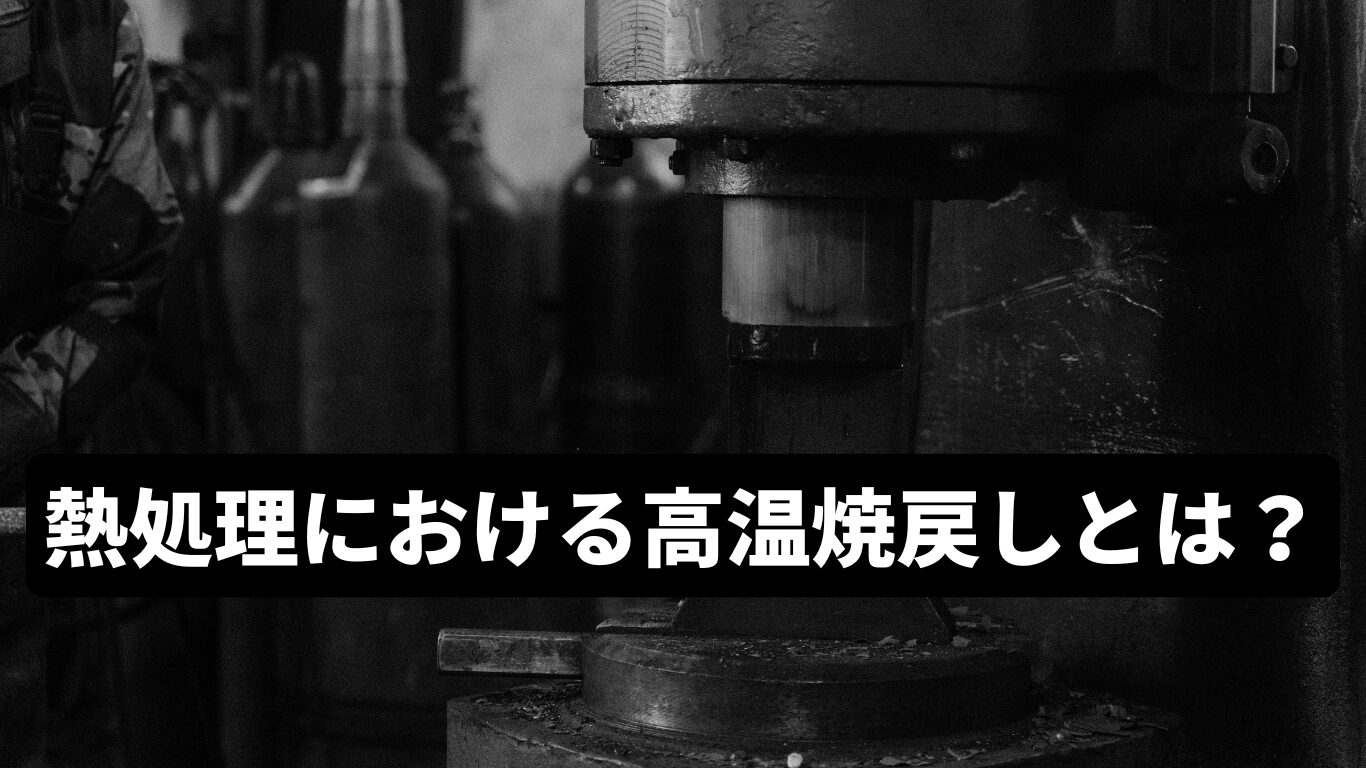
熱処理の専門知識をもっと深めたい方へ!今すぐ株式会社ウエストヒルの会社案内資料をダウンロードし、最新の技術情報と実績をご確認ください。
→ ウエストヒルの会社案内資料を無料ダウンロード
はじめに
製造業において、部品の性能や寿命を左右する重要な熱処理工程である高温焼戻し。300℃以上の高温域で実施されるこの処理は、材料の強度と靭性を理想的なバランスに調整することができます。自動車部品や産業機械部品など、高い信頼性が要求される製品に広く適用されているこの技術について、実践的な観点から解説していきます。
高温焼戻しの基本原理
温度域による組織変化
高温焼戻しでは、300℃から700℃の温度域で焼入れ材を加熱することで、組織を段階的に変化させていきます。300℃付近からセメンタイトの析出が始まり、400℃を超えると残留オーステナイトの分解が進行します。500℃以上では炭化物の球状化が促進され、マルテンサイトの分解が加速します。
この過程で、焼入れ直後の針状マルテンサイト組織は、より安定なフェライトと球状炭化物の組織へと変化していきます。600℃以上の温度域では、炭化物の粗大化が進むため、用途に応じた適切な温度設定が重要になります。
機械的性質への影響
高温焼戻しによる機械的性質の変化は、温度域によって大きく異なります。400℃付近までは硬さの低下とともに靭性が向上し、引張強さは緩やかに低下します。500℃を超えると、靭性の向上が著しくなり、伸びや絞りの値が大幅に改善されます。
特筆すべきは、一部の合金鋼で観察される二次硬化現象です。クロムやモリブデンを含有する鋼種では、500℃前後で一時的な硬さの上昇が見られます。引張強さと降伏点の比(降伏比)は、焼戻し温度の上昇とともに増加し、塑性変形能が向上します。
炭化物形成メカニズム
高温焼戻しにおける炭化物形成は、合金元素の種類と含有量に大きく依存します。一般的な炭素鋼では、ε炭化物からセメンタイト(Fe3C)への変化が主な反応です。合金鋼の場合、クロム、モリブデン、バナジウムなどの元素が特殊炭化物を形成します。
これらの特殊炭化物は、500℃以上の温度域で微細に分散析出し、強度の向上に寄与します。例えば、モリブデン鋼ではMo2Cが、クロム鋼ではCr7C3やCr23C6が形成されます。炭化物の大きさや分布は、最終的な機械的性質を決定づける重要な因子となります。
高温焼戻しの特徴と効果
靭性の改善効果
高温焼戻しによる靭性の改善は、最も重要な効果の一つです。焼入れ直後の脆い状態から、衝撃に強い粘り強い状態へと材質を変化させることができます。400℃以上の温度域では、マルテンサイトの分解と炭化物の球状化により、シャルピー衝撃値が大幅に向上します。
具体的には、焼入れ状態と比較して、シャルピー衝撃値は2〜5倍に増加します。低温での使用や、急激な負荷変動がある部品には、特に重要な特性改善です。靭性の向上は、疲労強度の改善にもつながり、部品の寿命延長に貢献します。
二次硬化現象
二次硬化は、特定の合金鋼で観察される興味深い現象です。500℃前後の温度域で、一度低下した硬さが再び上昇します。この現象は、特殊炭化物の析出によるもので、高温強度が要求される工具鋼や金型材料で積極的に活用されています。
例えば、SKD61などの熱間工具鋼では、550℃付近での焼戻しにより、HRC44〜46程度の高い硬さを維持しながら、優れた靭性が得られます。二次硬化を利用する場合、温度管理が特に重要で、±10℃以内の精度が必要です。
耐疲労性の向上
高温焼戻しによる耐疲労性の向上は、繰り返し応力を受ける部品の信頼性向上に直結します。適切な温度での焼戻しにより、疲労強度は20〜30%向上します。これは、内部応力の緩和と、微細な炭化物の均一分散による効果です。
回転部品や振動部品では、疲労強度の向上が特に重要です。例えば、クランクシャフトやコネクティングロッドでは、550℃前後での焼戻しにより、優れた疲労特性が得られます。表面粗さの影響も考慮し、仕上げ加工との組み合わせで最適な性能を引き出すことができます。
処理温度の選定基準
材質による適正温度
材質に応じた適正温度の選定は、高温焼戻しの成否を決める重要な要素です。炭素鋼の場合、炭素含有量により適正温度が異なります。0.4%C以下の低炭素鋼では550〜650℃、0.4〜0.6%Cの中炭素鋼では500〜600℃、0.6%C以上の高炭素鋼では450〜550℃が一般的な温度範囲です。
合金鋼では、含有元素の種類と量により、さらに細かな温度調整が必要です。例えば、クロム含有量が高い鋼種では、炭化物の安定性を考慮して、標準的な温度より20〜30℃高めに設定します。モリブデン鋼では、二次硬化を活用するため、500〜550℃の範囲で正確な温度管理が求められます。
目的に応じた温度設定
用途や要求特性に応じた温度設定も重要です。高い強度が必要な場合は、比較的低温の400〜500℃での処理が適しています。一方、靭性や延性の向上が主目的の場合は、550℃以上の高温域での処理が効果的です。
耐摩耗性が要求される部品では、二次硬化を利用した500〜550℃での処理が有効です。耐疲労性の向上には、500〜600℃の範囲が適しており、この温度域では適度な強度を維持しながら、内部応力の緩和効果が得られます。
二次硬化を考慮した温度管理
二次硬化を活用する場合、温度管理は特に重要です。最適な二次硬化温度は、合金元素の種類と量により異なります。例えば、Mo-V系高速度工具鋼では540〜560℃、Cr-Mo系熱間工具鋼では520〜540℃が二次硬化の最適温度域です。
温度管理の精度は、二次硬化を利用する場合、±5℃以内が望ましいです。これには、高精度な温度制御システムと、定期的な温度校正が必要です。昇温速度は2〜3℃/分程度とし、均一な加熱を確保します。
焼戻し時間の決定方法
部品サイズと保持時間
部品のサイズは、保持時間を決定する重要な要素です。基本的な目安として、断面積1cm²あたり2〜3分の保持時間が必要です。ただし、最低でも1時間以上の保持時間を確保することが推奨されます。大型部品では、断面積の増加に応じて保持時間を延長します。
例えば、直径50mmの丸棒では、最低1.5時間の保持時間が必要です。複雑な形状の部品では、最大肉厚部を基準に保持時間を設定します。急激な断面変化がある場合は、さらに20〜30%の余裕時間を加えることで、均一な焼戻しが可能になります。
合金元素の影響
合金元素は、焼戻し時の拡散速度に大きな影響を与えます。クロム、モリブデン、タングステンなどの元素は、炭素の拡散を遅延させる効果があります。このため、合金鋼では一般的な炭素鋼より30〜50%長い保持時間が必要です。
例えば、13Cr系ステンレス鋼では、炭素鋼の1.5倍程度の保持時間を設定します。高合金工具鋼では、さらに長時間の保持が必要で、標準的な保持時間の2倍程度を確保することもあります。二次硬化を利用する場合は、特に慎重な時間設定が重要です。
均一性確保のポイント
均一な焼戻しを実現するため、部品の配置方法や炉内の温度分布に注意を払う必要があります。部品間の間隔は最低30mm以上確保し、熱風の循環を妨げないようにします。大型部品と小型部品を同時に処理する場合は、熱容量の違いを考慮して配置を工夫します。
炉内の温度分布は、±10℃以内の均一性が望ましいです。これを確認するため、定期的な温度分布測定を実施します。強制循環式の炉を使用する場合は、ファンの回転数や風向きにも注意を払い、均一な加熱を確保します。
材質別の高温焼戻し条件
構造用鋼の処理条件
構造用鋼の高温焼戻しでは、用途に応じた適切な条件設定が重要です。機械構造用炭素鋼S45Cの場合、550〜650℃での焼戻しにより、適度な強度と靭性のバランスが得られます。保持時間は、断面積に応じて1〜2時間が標準的です。
クロムモリブデン鋼SCM440では、500〜600℃での処理が一般的です。この温度域では、モリブデンによる二次硬化の効果も得られます。焼入れ時の冷却速度との関係にも注意が必要で、油冷材と水冷材では最適な焼戻し温度が若干異なります。
工具鋼の処理条件
工具鋼の高温焼戻しは、二次硬化を活用するケースが多いです。SKD11などの冷間工具鋼では、500〜550℃での焼戻しにより、高い硬度と耐摩耗性が得られます。二次焼戻しを行うことで、より安定した特性が得られます。
熱間工具鋼SKD61では、550〜600℃での焼戻しが標準的です。この温度域では、高温での使用に耐える安定した特性が得られます。保持時間は1.5〜2時間とし、必要に応じて2回焼戻しを行います。
ステンレス鋼の処理条件
ステンレス鋼の高温焼戻しは、耐食性との兼ね合いが重要です。マルテンサイト系ステンレス鋼SUS420では、550〜650℃での焼戻しにより、適度な強度と耐食性が得られます。この温度域では、クロム炭化物の析出にも注意が必要です。
析出硬化型ステンレス鋼では、より複雑な熱処理サイクルが必要です。例えば、SUS630では、480〜620℃での時効処理により、高い強度と耐食性が両立できます。雰囲気管理も重要で、表面の酸化を防止するため、真空または保護ガス雰囲気での処理が推奨されます。
品質管理のポイント
硬さ測定方法
高温焼戻し後の品質確認では、硬さ測定が基本となります。ロックウェル硬さ試験(HRC)が最も一般的で、測定位置は部品の代表的な箇所を選定します。大型部品では、表面と中心部の硬さ差にも注意を払います。
測定回数は、1つの部品につき最低3点以上とし、測定値のばらつきが許容範囲内(通常±2HRC以内)にあることを確認します。定期的な硬さ計の校正も重要で、標準試験片による確認を月1回以上実施します。
組織観察の着眼点
金属組織の観察は、焼戻しの適否を判断する重要な手段です。光学顕微鏡による観察では、炭化物の形状や分布状態、マルテンサイトの分解状態を確認します。必要に応じて、電子顕微鏡による詳細観察も実施します。
観察試料の準備には特に注意が必要です。研磨後のエッチングには、一般的にナイタール(3%硝酸アルコール)を使用します。観察のポイントは、炭化物の大きさと分布の均一性、マルテンサイトの分解度合い、結晶粒界の状態などです。不適切な焼戻し条件では、粗大な炭化物の析出や、異常な組織が観察されます。
機械的性質の評価基準
高温焼戻し後の機械的性質は、用途に応じた適切な評価が必要です。引張試験では、引張強さ、降伏点、伸び、絞りの測定を行います。衝撃試験では、シャルピー試験による靭性評価が重要です。
特に重要な部品では、疲労試験による耐久性評価も実施します。評価基準は、部品の使用条件を考慮して設定します。例えば、高負荷を受ける部品では、降伏比(降伏点/引張強さ)が0.8以下であることが望ましいです。
トラブル対策と予防
焼戻し脆化の防止
焼戻し脆化は、特定の温度域で発生する靭性低下現象です。特に350℃付近(一次脆化)と500〜600℃(二次脆化)の温度域で注意が必要です。この現象は、粒界への不純物元素の偏析や、特定の炭化物の析出によって引き起こされます。
防止策として、これらの温度域での長時間保持を避けることが重要です。不純物元素(特にリン、硫黄)の含有量が少ない材料を選択することも効果的です。モリブデンの添加は、焼戻し脆化の抑制に有効です。
表面品質の確保
高温焼戻し時の表面品質劣化は、酸化スケールの生成が主な原因です。特に500℃以上の温度域では、酸化が急速に進行します。表面品質の確保には、適切な雰囲気管理が不可欠です。真空炉や保護ガス雰囲気炉の使用が推奨されます。
保護ガスとしては、窒素や、アルゴンなどの不活性ガスが使用されます。酸素濃度は50ppm以下に管理することが望ましいです。スケール除去が必要な場合は、ショットブラストや酸洗いなどの後処理を検討します。
変形制御の方法
高温焼戻しでの変形は、主に内部応力の解放によって発生します。特に複雑形状の部品や、薄肉部品では注意が必要です。変形を最小限に抑えるため、部品の支持方法や加熱・冷却条件の最適化が重要です。
支持具は、部品の熱膨張を考慮した設計が必要です。昇温速度は2〜3℃/分程度とし、部品全体が均一に加熱されるようにします。冷却時も同様に、急激な温度変化を避けることで変形を抑制できます。
設備選定と管理
炉の選定基準
高温焼戻し用の熱処理炉は、温度精度と均一性が重要な選定基準です。電気炉が最も一般的で、±5℃以内の温度制御が可能です。大型部品や量産部品では、連続炉の導入も検討します。
真空炉は、表面品質が特に重要な部品に適しています。雰囲気炉は、酸化防止と同時に、特殊な表面処理効果も期待できます。いずれの炉種でも、温度分布の均一性と、制御性の高さが重要です。
温度制御の重要ポイント
温度制御は、焼戻し品質を左右する重要な要素です。複数のゾーンに分けた温度管理により、均一な加熱を実現します。温度センサーの定期的な校正と、制御システムの保守が必要です。
プログラム制御による自動運転では、昇温・保持・冷却の各工程を最適化できます。温度記録は、トレーサビリティの観点から重要で、デジタルデータとして保存することが推奨されます。
メンテナンス項目
定期的なメンテナンスは、設備の信頼性維持に不可欠です。ヒーターの点検、断熱材の劣化確認、シール部品の交換などが主な項目です。真空炉では、真空度の確認と、ポンプのメンテナンスも重要です。
日常点検では、温度制御系の動作確認、安全装置の確認を実施します。年次点検では、より詳細な点検と、必要な部品交換を行います。予防保全の観点から、定期的な部品交換計画を立てることが推奨されます。
コスト最適化の方法
エネルギー効率の向上
エネルギーコストの削減には、炉の断熱性能維持と、運転方法の最適化が重要です。断熱材の劣化は、外表面温度測定により判断できます。表面温度が室温+40℃を超える場合は、断熱材の補修を検討します。
バッチ編成の工夫も効果的です。炉の容積に対して、70%以上の装入率を目指します。ただし、温度均一性を損なわない範囲で調整が必要です。夜間電力の活用も、コスト削減に有効です。
生産性の改善方法
生産性向上には、処理時間の短縮と、作業効率の改善が重要です。前処理工程からの連携を強化し、待ち時間を削減します。同種材料・同サイズの部品をまとめて処理することで、生産効率を向上させます。
自動化設備の導入も検討に値します。プログラム制御による無人運転や、搬送装置の導入により、作業効率が向上します。ただし、品質管理面での配慮は必要です。
ランニングコストの削減
ランニングコストの削減には、総合的なアプローチが必要です。保守コストの削減には、予防保全の徹底が効果的です。定期的な点検と部品交換により、突発的な故障を防止できます。
消耗品の使用量管理や、保護ガスの回収・再利用なども有効です。作業標準の整備により、作業効率を向上させることもできます。設備の稼働率向上と、エネルギー効率の改善を両立させることが重要です。
まとめ
高温焼戻しは、鋼材の機械的性質を最適化する重要な熱処理工程です。適切な温度・時間管理と、品質管理の徹底により、安定した特性を持つ製品を生産できます。本記事で解説した技術的なポイントを押さえることで、品質とコストの両面で優れた生産体制を構築できます。特に、材質に応じた条件設定、品質管理の徹底、トラブル対策の実施が重要です。これらの知識を活用し、高品質な製品製造を実現してください。
会社案内資料ダウンロード
熱処理の詳細をもっと知りたい方へ!株式会社ウエストヒルの会社案内資料を今すぐダウンロードして、私たちのサービスと実績を確認してください。電気炉・装置・DIVA・SCRなどの熱処理設備や環境のご紹介、品質管理、施工実績など、あなたの課題解決をサポートする情報が満載です。